Emerging technology in human robot collaboration (HRC) has transported dreams into reality, particularly in the arena of smart lightweight robots that are transforming the lives of individuals with mobility issues, and improving the quality of daily work in many application scenario. Direct, physical interaction between a human and a robot has potential to provide assistance (as well as rehabilitation) which can extend the human user’s physical capabilities.
FourByThree represents a major step forward the possibility to tailor the robot on the real needs of the persons, creating modular devices that augment their capacity.
However, the adoption of lightweight robots opens important Ethics problems related to how to guarantee the human safety: to be successful, the robot must be able to realize the system-level objectives without compromising the subject’s safety in every possible usage condition.
The FourByThree aims at scattering the common approaches by widely adopting serial-elastic-actuators for moving and controlling the robot chain. Indeed, when it comes to the mechanical interface between motors and loads, “the stiffer the better” is a traditional premise of good design, but it is far to be optimal particularly for cooperative robots, because elasticity can be used for a wide variety of purposes, and especially for safety.
Figure 1: Control of a Kinematic chain through series elastic actuators
One effect of the series elasticity is to low-pass filter shock loads, thereby greatly reducing peak gear forces. The proper amount of interface elasticity can substantially increases shock tolerance while maintaining adequate small motion bandwidth.
Although compliance can help improve safety, it must coexist with other system objectives. In many cases, the system is to track a desired trajectory, e.g. to assist in a defined task. The more complex dynamics of compliant actuators requires proper model selection and controller design to give satisfactory performance. However, in traditional motion control, compliance is usually minimized in both the drivetrain and controller design to reduce mechanical resonance and improve rejection of load-side disturbances.
To consider the effects of the elastic element, a model for the series elastic actuator with load-side dynamics has to be introduced, validated, and then used for controller design.
The performance and safety of several control architectures are therefore the core of the control activities in FourByThree project.
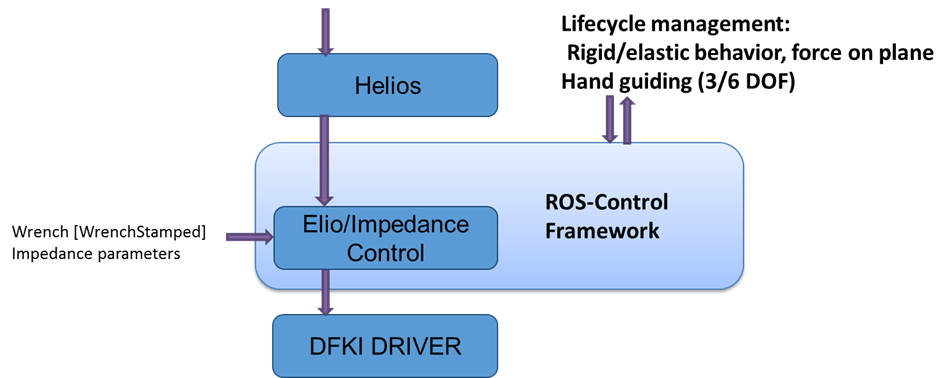
Figure 2: the overall FourByThree architecture
Implicit in the design of the controllers is the avoidance of “high-gain feedback control”. Although disturbance observers and other advanced loop-shaping techniques may be able to provide improved performance, any sort of high-gain feedback can be dangerous in the event of a hardware malfunction or other system error. Another consideration for real-world implementation of any compliant actuator is unmodelled dynamics or disturbances. For unmodelled dynamics on the subject side, these forces will affect the system the same as the subject interactive torques. Without any distinguishing characteristics (e.g. different frequency bands), it is difficult to separate these disturbances from the subject’s input. Especially in low-stiffness implementations, this may compromise the system performance, so careful modelling and feedforward compensation is critical.
FourByThree, therefore, aims at tackling the problem through two concurrent actions: to develop innovative motion planner, that minimizes the dynamics disturbances for the control; to develop advanced control strategies – based on the inversion of the system dynamics – to grant large controllable bandwidth.
Such modules are named HELIOS – the smooth motion interpolator – and ELIO – the advanced coupled centralized axes controller. HELIOS and ELIO have been designed in order to increase dramatically the potential field of application of the FourByThree robot: the robot will be able to track trajectories in the Cartesian space accurately, and to react fast and robustly to external forces, allowing high-quality force control tracking.
Around this powerful engine, different high-level controllers can be therefore applied to improve the human capabilities while executing cooperative industrial tasks: vision servoing modules as well as hand-guiding modules can be just plugged as additional functionalities.
Figure 3: Advanced Learning and Adaptive Strategies for High-level Interaction modalities
Further, FourByThree robot will be provided by innovative algorithms also for the hand-guiding. Indeed, a standard manual guidance with gravity and friction compensation does not directly allow the compensation of an unknown manipulated component weight (i.e., requiring an external observer to estimate the inertial properties of the manipulated part).
The FourByThree robot will be provided by adaptive impedance controllers based that autonomously will continuously update the real-time the set point of the impedance control based on the user-applied forces at the user-interface (e.g., an handle at the robot end-effector). The proposed control law allows to perform fine positioning of the robot by applying small forces, while allows a fast/large motion positioning of the robot by applying higher forces. Moreover, based on the derivative of the user-applied forces and of the measured Cartesian velocities, a switching logic has been implemented in order to enable/disable the empowering adaptive manual guidance control strategy, allowing compensating for the manipulated component weight during both the motions and the steady states.
FourByThree robot, therefore, will be not only a modular robot in term of HW solutions, but the control architecture itself will be the core that make the robot modular in term of the potential expandability of its functionalities to many different application requirements. FourByThree robot will make affordable the assembly of unique products or products with a small-scale lot size and large-scale lot size with a high diversity of variants, many manufacturing steps that are nowadays difficult or non-economic to automate. The robot will be a real assistance system, and the hybridization of biological and technical systems, a so-called “Human Hybrid Robot” (HHR) will be enabled by the high-performance in position and force tracking of the FourByThree robot.